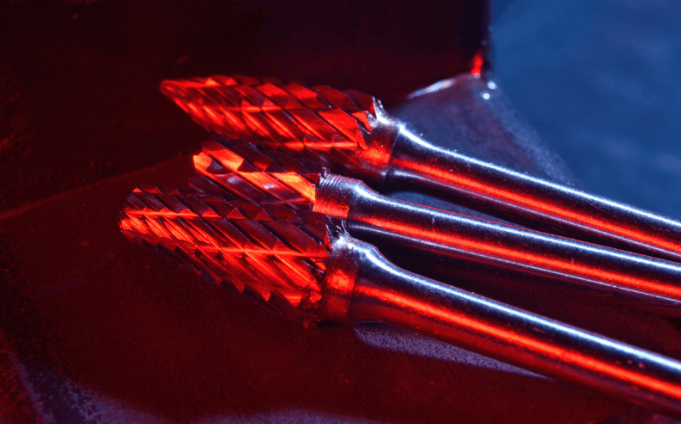
Cutting carbide, particularly tungsten carbide, can be challenging due to its extreme hardness and brittleness. Commonly used in industrial tools, drill bits, carbide dies, and wear-resistant parts, carbide requires specialized techniques to cut without cracking or damaging the material.
If you’re a machinist, fabricator, or DIY enthusiast interested in knowing how to cut carbide effectively, this guide covers the best tools, step-by-step methods, and expert tips for getting clean, precise results.
Understanding the Challenge
Tungsten carbide ranks among the hardest materials used in manufacturing, second only to diamond. This characteristic raises an important question: can you cut tungsten carbide? The short answer is yes—but it requires the right tools and techniques.
Unlike softer metals, tungsten carbide’s extreme hardness makes it resistant to conventional cutting methods. Standard steel blades will dull almost immediately, and excessive force can cause cracking or chipping. Additionally, the material’s brittleness means improper handling leads to microfractures, compromising structural integrity.
However, specialized tools make cutting tungsten carbide possible. These methods minimize heat buildup and mechanical stress, ensuring clean cuts without damaging the workpiece. Let’s learn more about them in the next section.
Best Tools for Cutting Carbide
Carbide cutting demands specialized equipment that can withstand its extreme hardness. Below are the most effective tools for the job, each suited for different applications and precision levels:
Diamond-Coated Tools
Diamond-coated blades and grinding wheels are the gold standard for clean and precise cuts. The diamond abrasive effortlessly grinds through tungsten carbide without excessive heat buildup. These tools work best for detailed shaping and finishing work where precision matters most.
Carbide-Tipped Saws
Carbide-tipped saws are a cost-effective option for carbide tooling maintenance when diamond blades are unavailable, although they are less durable. These saws can make straight cuts in smaller carbide pieces but require more frequent blade replacements compared to diamond options.
Waterjet Cutting
Unlike cold headings, which shape carbide without heat, waterjet cutting removes material cleanly for the finished edges. The high-pressure water-abrasive mixture eliminates the risk of thermal damage and works well for thicker carbide pieces.
Abrasive Cutoff Wheels
Abrasive wheels are a more budget-friendly option that can handle carbide cutting at slower speeds. Although they require more time and produce rougher edges than diamond tools, they get the job done for less demanding applications.
Now that you know which tools to use, let’s walk you through the step-by-step process for cutting carbide safely and effectively.
How to Cut Tungsten Carbide: A Step-by-Step Guide
Cutting tungsten carbide requires careful technique to avoid damaging the material and your tools. Follow these steps for clean and safe results:
Step 1: Choose the Right Tool
The first step in successfully cutting tungsten carbide is choosing the right tool. Diamond blades are ideal if you want precision. If cost is a concern, abrasive wheels are a practical option.
A waterjet is the most effective solution for thick carbide sections. To achieve clean and precise results, make sure the tool’s hardness is comparable to the carbide being cut.
Step 2: Secure the Workplace
Firmly clamp the carbide workpiece in place to prevent vibrations that can lead to uneven cuts. Doing so minimizes the risk of the material cracking due to unexpected movement during the cutting process.
Moreover, a securely held workpiece significantly reduces safety hazards, such as the carbide slipping and causing injury. Remember, taking the time to secure your workpiece properly is crucial for achieving optimal results and maintaining a safe working environment.
Step 3: Apply Lubrication/Coolant
Using the right coolant during the cutting process drastically reduces heat buildup, which can compromise the carbide’s strength and lead to damage. Coolant also extends the lifespan of your cutting tools, saving you money and time on replacements.
As a bonus, coolant helps you achieve a cleaner, higher-quality cut by minimizing friction and preventing material deformation. So, make sure the coolant you select is compatible with both the carbide and the cutting tool you’re using.
Step 4: Make the Cut
When cutting tungsten carbide, we recommend adopting a measured and patient approach. Apply slow, steady pressure and let the tool work at its optimal speed to achieve clean, precise cuts and extend the life of your cutting equipment. For thicker pieces, use multiple light passes instead of a single heavy cut to minimize the risk of damage and produce a smoother, more accurate result.
Step 5: Inspect and Finish
After cutting, inspect the carbide under magnification for any micro-cracks. If necessary, smooth out any rough edges with diamond files to achieve a polished finish. Finally, ensure all abrasive debris is cleaned away from the workpiece and the surrounding area, as these particles can cause damage or interfere with subsequent processes.
Common Carbide Cutting Mistakes and How to Avoid Them
Even experienced professionals can encounter challenges when cutting tungsten carbide. Avoiding these pitfalls will help you achieve better results while extending your tool life:
Using the Wrong Cutting Tools
One of the most frequent mistakes is attempting to cut carbide with standard steel blades or inappropriate equipment. These tools will dull quickly and can even shatter with excessive force. To prevent this from happening, always use tools specifically designed for carbide cutting, such as diamond-coated tools, carbide-tipped saws, or specialized abrasives.
Applying Too Much Force or Speed
Using excessive force or speed generates too much heat, which causes microfractures, premature tool wear, and dangerous kickbacks. To avoid this, let the tool work at its recommended speed and apply gentle, consistent pressure for clean, precise cuts and longer tool life.
Neglecting Proper Cooling
Skipping coolant during the carbide-cutting process is a mistake with serious consequences. Without proper lubrication, carbide is susceptible to thermal shock, which can compromise its structural integrity.
Neglecting to use coolant also accelerates tool wear, leading to premature failure and the need for frequent replacements. To avoid these issues, always use the appropriate cutting fluid or coolant, especially when grinding or making prolonged cuts.
Poor Workpiece Securement
Improperly securing the workpiece during cutting can lead to vibrations and movement, resulting in uneven cuts, chipped edges, and potential damage to both the workpiece and the cutting tool.
In some cases, it can even cause the workpiece to break free, posing a significant safety hazard. To avoid these problems, always ensure the carbide workpiece is firmly clamped or secured to a stable surface before starting any cutting operation.
Ignoring Safety Precautions
Carbide cutting generates fine dust and sharp fragments that can pose serious health risks if inhaled or come in contact with your eyes. Overlooking safety measures like wearing eye protection (safety goggles) and respiratory masks can lead to eye injuries, respiratory problems, and long-term health complications. Additionally, inadequate workshop ventilation can allow harmful dust to accumulate, further increasing the risk of exposure.
To prevent these issues, every carbide-cutting operation should follow the same safety protocols as working with glass or ceramics. Always wear safety goggles and a respiratory mask, and ensure your workspace is properly ventilated to minimize dust inhalation.
Alternative Methods for Shaping Carbide
While cutting is often the go-to method for working with carbide, several alternative approaches may better suit specific applications. These techniques prove particularly useful when precise shaping is needed or when cutting would compromise the material’s integrity:
Grinding for Precision Finishing
When ultra-fine tolerances matter more than bulk material removal, grinding offers superior control. Diamond grinding wheels can shape carbide with remarkable accuracy, creating sharp edges and smooth surfaces that cutting alone can’t achieve. This method shines for finishing tool bits or creating precise angles on carbide inserts.
Brazing for Assembly Applications
Instead of cutting large carbide pieces, many fabricators braze smaller carbide tips to steel bases. This hybrid approach combines carbide’s wear resistance with steel’s toughness, creating composite tools like drill bits or milling inserts. The process requires specialized equipment but eliminates the need for difficult carbide cutting in many cases.
Electrical Discharge Machining (EDM) for Complex Geometries
EDM provides a superior alternative for intricate shapes that would be impossible with mechanical cutting. The non-contact process uses controlled electrical sparks to erode the material, allowing for incredibly detailed work without inducing mechanical stress. This method excels when creating custom tooling or molds from solid carbide blanks.
Understanding these alternatives and knowing when to use them completes your toolkit for working with carbide. Choosing between cutting, grinding, or other methods depends on your specific project requirements and available equipment.
Key Takeaways
Cutting carbide requires specialized tools, proper techniques, and safety precautions to avoid damage. You can confidently tackle carbide-cutting tasks by following the steps and best practices outlined in this guide.
Need high-quality carbide dies, cutting tools, or expert advice? Visit our website to explore our premium carbide solutions and get professional support for your next project. Contact us today!