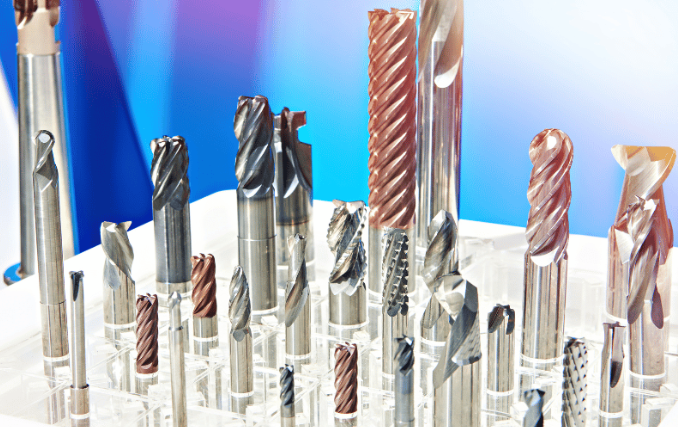
Carbide dies play a critical role in metalworking, known for their durability in shaping, cutting, and forming tough materials. That said, their lifespan isn’t fixed—it can range from a few months to several years, depending on how they’re used and maintained. The average lifespan of carbide dies depends on factors like material hardness, production volume, and die design, but many dies fail early due to preventable mistakes.
In this guide, we’ll cover the most common errors that shorten die life—and more importantly, share proven carbide die usage tips to help you extend performance and reduce downtime. If you work in manufacturing or handle tool maintenance, these tips will help you get the most out of your carbide dies.
Common Mistakes That Reduce Carbide Dies’ Lifespan
Even the toughest carbide dies can fail early when exposed to avoidable errors. While these tools are engineered for long-term use, the carbide dies lifespan often falls short due to common misuse, including:
Poor Handling & Storage
Improper handling and storage can cause irreversible damage. Dropping or roughly handling carbide dies may create micro-fractures that worsen over time, eventually leading to breakage. Just as critical is how they’re stored—humidity can cause corrosion, and careless stacking may chip the edges. These issues, while seemingly minor, can reduce the lifespan of your carbide dies by 30–50%.
Incorrect Lubrication Practices
Using the wrong lubricant—or using it incorrectly—is another common reason for premature failure. Applying too much lubricant can lead to residue buildup, while too little increases friction and wear. Even selecting a lubricant not suited for the material can cause uneven wear. These mistakes often result in shortened die life and increased downtime.
Overloading and Improper Usage
Many users unknowingly shorten the lifespan of their carbide dies due to operational misuse. Common issues include:
- Exceeding the recommended tonnage limits
- Running dies at the wrong speeds
- Processing materials that the die wasn’t designed for
These practices create stress points that can lead to cracks and structural failure. For instance, a die built for aluminum might last years under the right conditions, but if used on stainless steel, it could fail within weeks.
Neglecting Regular Maintenance
Skipping routine maintenance lets small problems snowball into serious damage. Failing to clean the dies after use allows metal debris to build up, which creates a rough surface that wears down precision over time. Ignoring early signs of wear, like galling, can also cause permanent damage and force early replacement.
Regular inspections are essential. They allow you to catch and fix issues before they result in unplanned downtime or costly repairs.
Improper Sharpening and Reconditioning
When maintenance is done incorrectly, it often does more harm than good. Common sharpening mistakes include:
- Removing too much material
- Using the wrong grinding angles
- Creating uneven cutting edges
These errors compromise structural integrity and throw off critical tolerances. Unlike steel, carbide must be handled with exacting precision. Up next, we’ll share carbide die usage tips to help you avoid these pitfalls and get the most out of your tools.
How to Extend Carbide Dies Lifespan
Now that we’ve identified the common mistakes that shorten die life, let’s focus on proven strategies to maximize your carbide dies’ performance and longevity. Implementing these practices can significantly extend your tooling’s productive lifespan while maintaining consistent quality in your operations:
Optimize Handling and Storage
Proper care of carbide dies is essential for ensuring their long lifespan and continued effectiveness. Here’s how to handle and store them correctly:
- Use protective cases or foam-lined containers during transport to prevent impact damage.
- When storing carbide dies long-term, maintain a controlled environment with stable humidity levels below 50% and temperatures between 60-80°F.
- Consider using desiccant packs in storage cabinets to absorb moisture, and organize dies vertically in labeled racks to prevent edge damage from stacking.
These simple measures can preserve your dies’ structural integrity during downtime.
Implement Precision Lubrication Practices
To prevent operational issues, you need to implement precision lubrication practices following these guidelines:
- Select lubricants specifically formulated for your processed material – whether it’s aluminum, steel, or specialty alloys.
- Apply lubricant in thin, even coats using spray systems or precision applicators, ensuring complete coverage without excess buildup.
- Establish a schedule based on production volume, and always clean dies thoroughly before reapplying lubricant.
- For high-temperature applications, consider graphite-based or synthetic lubricants that maintain viscosity under extreme conditions.
Master Proper Usage Techniques
Proper usage habits lead to long-term performance and fewer replacements, saving both time and money. Here are some key carbide die usage tips you can put into practice:
- Operate within the manufacturer’s recommended pressure and speed limits, and use tonnage monitors if available.
- Select dies designed for the specific material being processed, and consult the manufacturer before using a die on a harder alloy than intended.
- Track die wear and tear through production monitoring, and rotate multiple dies in high-volume applications for even wear distribution.
Establish Rigorous Maintenance Routines
Preventive maintenance is also key to extending the lifespan of your carbide dies. The following are steps you can incorporate into your routine:
- After each production run, clean dies thoroughly using specialized solvents and soft brushes to remove metal particles and lubricant residues.
- Conduct weekly visual inspections under proper lighting, using magnification tools to detect early signs of wear, galling, or micro-fractures.
- Maintain detailed maintenance logs for each die, tracking usage hours, maintenance activities, and performance trends. This data becomes invaluable for predicting remaining service life and planning replacements proactively.
Apply Professional-Grade Sharpening
Keeping carbide dies sharp is necessary for efficiency and high performance in metalworking operations. Here’s how you can do so with precision:
- Only use diamond grinding wheels on carbide tooling. Other abrasives can cause tiny cracks or microfractures that mess up the die.
- When sharpening, stick to the original angles and shapes of the cutting edges. Only remove enough material to get the edge back.
- For complex dies or major wear and tear, it’s best to get a qualified tooling specialist to handle it. They have the skills and tools to regrind the die precisely without messing it up.
- Instead of waiting until the die is obviously worn down, set up a regular sharpening schedule based on how much you use it.
Leverage Advanced Monitoring Technology
Modern tooling management benefits greatly from technological advancements. Here’s how you can integrate them to enhance your carbide die management processes:
- Implement vibration analysis systems to detect early signs of die fatigue and prevent unexpected failures and costly downtime.
- Use laser measurement tools to track dimensional changes in your dies over time.
- Digital tracking systems can automate maintenance scheduling based on actual usage data rather than estimates.
Investing in these monitoring technologies can lead to significant cost savings by extending tool life and minimizing disruptions in your operations. In the penultimate section, we’ll provide more specialized tips to further optimize carbide die performance.
Additional Carbide Die Usage Tips
Although the average lifespan of carbide dies mainly depends on application specifics, adhering to these strategic practices can substantially extend their longevity:
Rotate Dies in High-Volume Production
One of the most effective carbide die usage tips for high-volume operations is to implement a die rotation system. Rotating your dies helps distribute wear more evenly and prevents one tool from taking the brunt of the workload. By cycling through your inventory strategically, you maintain consistent output quality and extend the average lifespan of carbide dies across your entire setup.
Prioritize Quality in Die Selection
When sourcing new carbide dies, quality matters more than you might think. Always check for proper material certifications and ask for manufacturer testing data to confirm you’re getting the right carbide grade for your needs.
For more demanding jobs, consider specialty coatings like titanium aluminum nitride (TiAlN) or diamond-like carbon (DLC). These coatings improve wear resistance and boost tool longevity. While high-end dies may cost more upfront, they pay off with fewer replacements, less downtime, and lower long-term costs.
A high-quality die tailored to the right material can last three to five times longer than lower-grade options, making it a wise investment for any serious operation.
Establish a Die Tracking and Documentation System
Digital tracking is one of the most overlooked but impactful carbide die usage tips. By logging usage hours, maintenance records, and performance benchmarks, you can schedule maintenance proactively and spot wear trends before they lead to failure.
This documentation reduces unexpected die failures by 30–40%, helps justify premium tooling investments, and keeps all operators aligned with standardized best practices. Instead of relying on guesswork, you’ll have data-driven insights that extend the average lifespan of carbide dies and improve shop floor efficiency.
Implement a Preventive Maintenance Schedule
A well-structured preventive maintenance program goes a long way in protecting your tooling investment. This includes routine cleaning after every use, scheduled inspections, and planned replacements based on real usage data.
Tracking wear and maintaining ideal operating conditions reduces the risk of unexpected breakdowns and ensures consistent part quality. Staying ahead of maintenance needs is one of the smartest ways to preserve die integrity and maximize return over time.
Invest in Operator Training Programs
Even the best carbide dies will underperform in the wrong hands. That’s why training is essential. A comprehensive training program should cover three critical areas: proper die installation and alignment, optimal run settings for different materials, and recognizing early signs of wear.
Trained operators make better decisions in real time, reducing stress on the dies and preventing unnecessary damage. Over time, this operational discipline translates into longer die life, fewer replacements, and fewer production interruptions.
Key Takeaways
The average lifespan of carbide dies depends on multiple factors—quality, proper usage, and routine maintenance being the most critical.
By avoiding common mistakes and following proven carbide die usage tips—like careful handling, correct lubrication, preventive maintenance, and proper sharpening—you can extend tool life, reduce downtime, and cut replacement costs.
That said, all dies eventually reach the end of their service life. When they do, professional reconditioning or replacement is the best way to maintain performance and keep operations running smoothly.Need help getting the most out of your carbide tooling? The team at Raven Carbide Die is ready to support your operation. Schedule a consultation today and let’s keep your tools working at their best.